Carbon footprint
"OBJECTIVE MINUS 30 BY 2030"
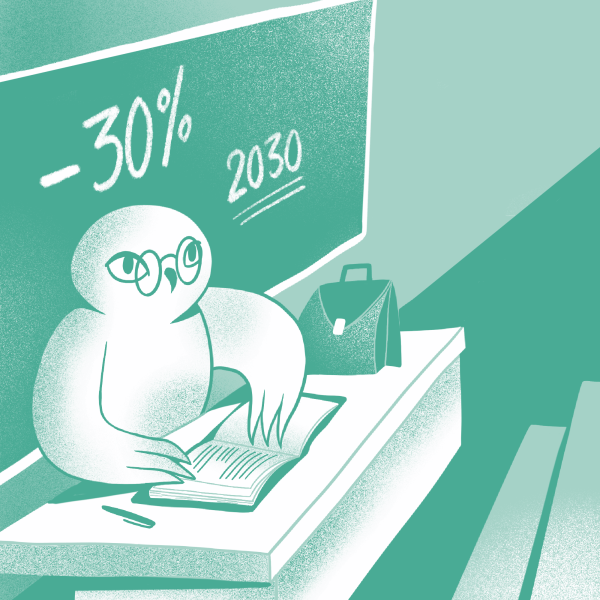
"Our brand has set itself the target of reducing its environmental impact by 30% for each pair of skis produced by 2030. That's the challenge we've set ourselves for the next 10 years in the context of the ZAGREEN program."
Indeed, based on our impact in 2019, we found that the production of a pair of skis produces an average of 116kgCO2eq.
By 2030, our aim is to reduce the 2019 figure to an average of 80kgCO2eq per pair of skis, i.e. an impact reduced by 30% over 10 years.
As ZAG is a growing company, we have decided to focus on the impact of our pairs rather than that of the company as a whole. Nevertheless, we have set ourselves the goal of controlling the impact of our growth, and thus reducing it in relation to our products.
In our view, this 30% project is 100% achievable, and it would not be surprising if we were to exceed this target and reduce our impact even further.
OUR CURRENT CARBON FOOTPRINT VS. 2030 TARGET
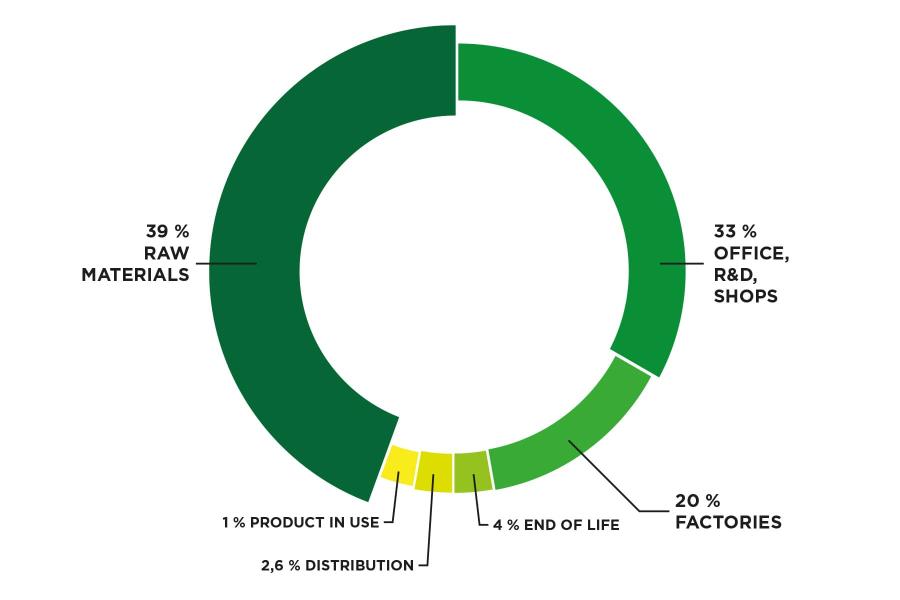
After a study of our carbon impact, we found that the 3 main sources for ZAG are: raw materials, headquarters/offices/lab and factories, so it's on these 3 main items that our work will focus.
Raw materials
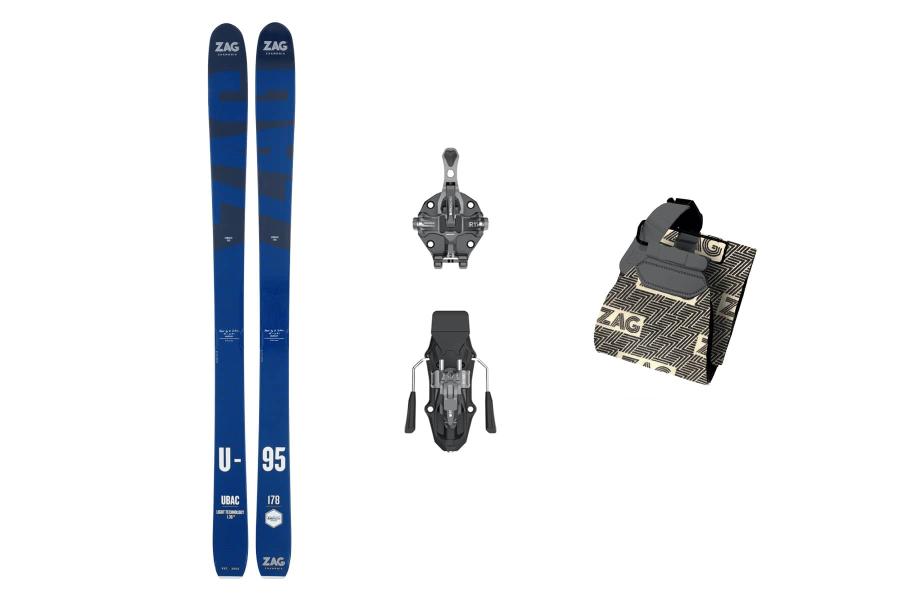
Our number 1 impact is everything we use in the skis, skins and bindings we sell.
As far as sealskins and bindings are concerned (which represent 44% of the total impact of raw materials), we will continue to work with companies committed to the environmental cause, with values that match our own, such as the POMOCA brand, which produces our sealskins not far from our mountains in the Lausanne area, and which is therefore in line with our ecological approach.
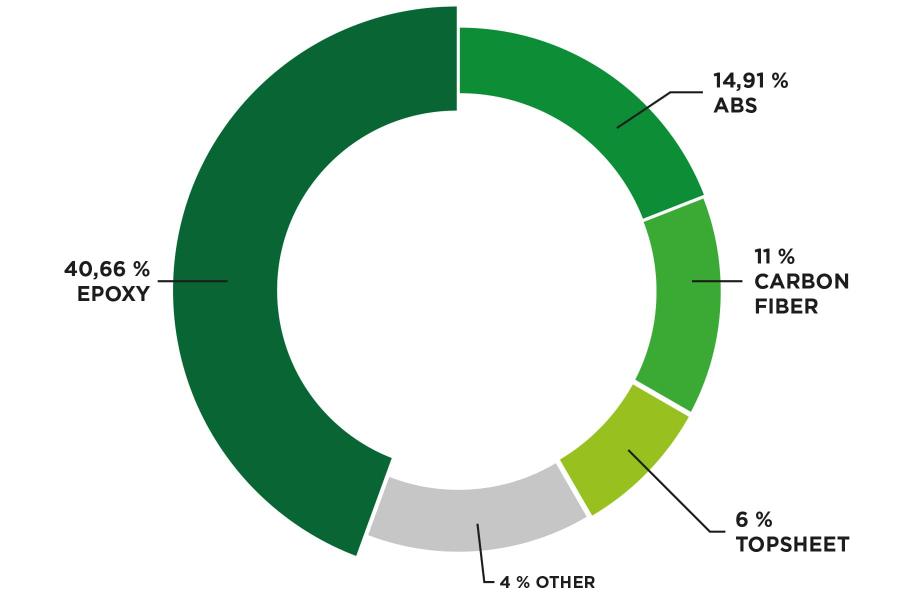
Epoxy resin: The most impacting raw material (40%).
Today, we also use small quantities of biosourced resins at 33% and 25%. In equal quantities, this resin has 40% less impact than its compatriot, epoxy resin.
Objective 2030: Switch all our skis to 33% biobased resin and use at least 50% biobased resin for a significant proportion of production.
ABS: 2nd most impacting material, but miles away from epoxy resin.
Objective 2030: Find a more responsible alternative.
Carbon fiber: 11% impact, but only 1% of the total impact of raw materials.
Objective 2030: A material that is difficult to replace, we are currently working on substitutes to offer you touring skis that are as light and high-performance as ever.
Topsheet: Big impact in terms of quantity used.
Objective 2030: At present, we're waiting for feedback from tests to see if the solution we've devised is sustainable over time.
Energy and factory
20% of our carbon footprint is generated by our factories, particularly in the processing of raw materials.
As we aim to produce mainly in Europe (90%), our partner factories are located in Poland and Tunisia. It should be noted that there are a limited number of factories in Europe, all of which are heavily used. It is therefore complicated on our scale to monitor the impact of our factories.
Objective 2030 :
Our aim is for our current partners to be able to produce between 20% and 40% of their energy using clean, more environmentally-friendly means than the current large-scale solutions used in their respective countries (installation of solar panels, recovery of wood shavings for heating, closed water circuits, etc.).
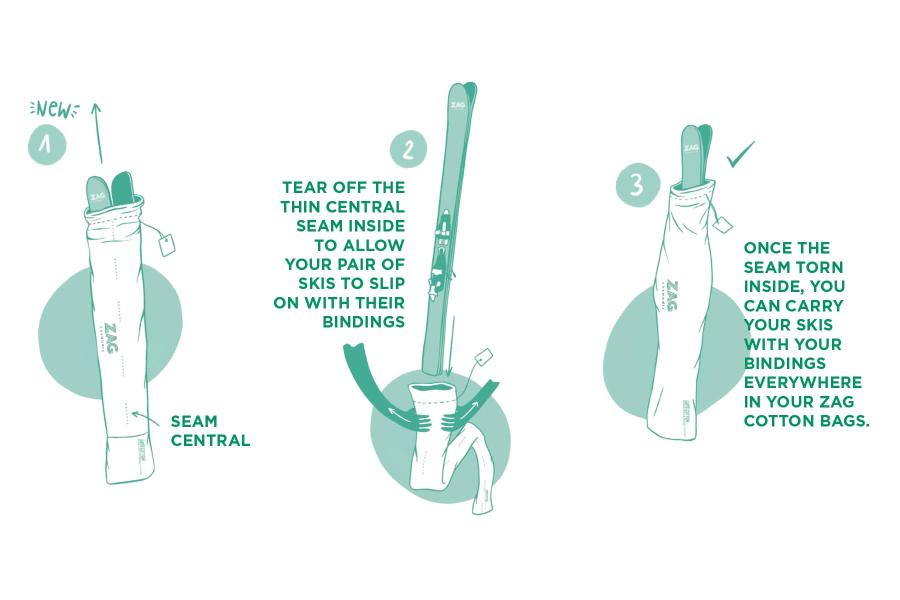
Plastic blisters : this is the plastic packaging that holds your new skis. We've already made some progress in this area, since this winter skis have been packaged in reusable pouches that can be used as protective covers and/or fabrics for anything you can imagine and make.
Objective 2030 : Find a solution that is even more respectful of the environment, notably through material sourcing.
Soles : Starting this season 23/24, we're launching a sole that's 85% recycled, using scraps from the manufacture of other soles by our suppliers. It concerns the HARFANG and UBAC ranges.
Objective 2030 : Produce 50% of our production with recycled soles (objective achieved).
Headquarters - Offices - Lab - Store
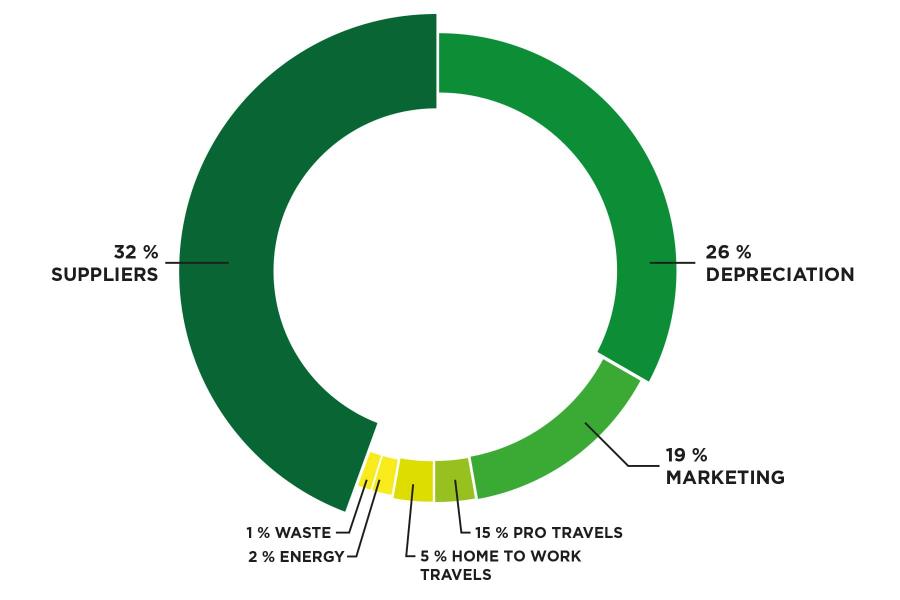
Here, our biggest impact comes from supplier expenditure, i.e. all the physical or intangible products we buy so that the company can carry out its business. In order to reduce this impact, our 2030 objective will be to rationalize these purchases and target companies that share our convictions.
It is not in this sector that the biggest impact gains will be made, even if measures are planned such as telecommuting 3 days a week (for all possible positions) or rationalizing our digital and marketing actions.